您现在的位置是:首页 > 电气技术 > 电气技术
风力发电机常见故障诊断方法
来源:艾特贸易2017-03-18
简介风力发电机常见故障诊断方法 风力发电机发电的原理,是利用风力带动风车叶片旋转,再透过增速机将旋转的速度提升,来促使发电机发电。依据目前的风车技术,大约是每秒三公尺的
风力发电机常见故障诊断方法
风力发电机发电的原理,是利用风力带动风车叶片旋转,再透过增速机将旋转的速度提升,来促使发电机发电。依据目前的风车技术,大约是每秒三公尺的微风速度(微风的程度),便可以开始发电。下面是风力发电机的故障及故障诊断方法!
1、传动链失效
风机的传动链由叶轮、主轴、主轴轴承、齿轮箱,联轴器五部分组成,其中以齿轮箱、主轴轴承出现的出现故障最多。常见故障主要有齿轮损伤(齿面磨损、齿面胶合和擦伤、齿面接触疲劳、弯曲疲劳与断齿),轴承损坏(磨损失效、疲劳失效、腐蚀失效、断裂失效、压痕失效、胶合失效),轴的故障(断轴,轴弯曲,轴向轴不对中)。
(a)叶片
叶片为风力发电机的主要承受风组件,在风力发电机正常运行环境下,叶片的振动形式为低频大振幅运动。
(b)轮毂
轮毂为连接叶片和主轴的部件,其受力是通过叶片传递过来,由于风况的多变性,造成其受力变化频繁,当受到大于极限载荷的力时,其失效多为轮毂的整体断裂。通常通过ANSYS和MSC等有限元分析软件对其进行静强度的分析和疲劳分析,而振动对其影响不大。
(c)增速箱
增速箱是受振动相对影响最大的一个。由于风力发电机工作环境恶劣,其破坏率高达40阶50%,同时对风力机的定期检修和定期维护的难度大、费用高,所以对风力发电机组的故障诊断和预知维修就显得更加迫在眉睫。
风力发电机组的振动故障发生在主传动链上,其从输入的主轴开始到发电机均为旋转机械部件。常规的振动故障特征多为:
cl)转轴组件故障:转子不平衡,转子不对中,转子弯曲,油膜涡动,油膜振荡,转轴裂纹,喘振。
c2)滚动轴承转动振动:轴承结构特点及加工装配误差,运动故障引起振动(磨损、表面损伤),滚动轴承故障特征频率,轴承元件固有频率。
变速箱中的主要部件有齿轮、轴承、轴及箱体,轴承故障占变速箱故障的19%,所以研究轴承故障诊断的研究对研究变速箱故障诊断具有重要的意义。轴承由外圈、内圈、滚动体和保持架组成,轴承在使用中会磨损出现疲劳剥落和裂纹等故障。产生故障的轴承在工作中,滚动体每经过一次故障部位,就会产生一次冲击。
c3)齿轮的振动分析:齿轮的故障(弯曲疲劳与断齿、齿面磨损、齿面胶合和划痕、齿面的接触疲劳)。
c4)齿轮的振动特点:与一般的回转机械相比,齿轮振动具有如下几个显著特点:
l)较高的振动特征频率。齿轮振动的特征频率主要为其啮合频率及其倍频成分,对于石化行业等高速回转机组的齿轮箱而言,一般达5000-10000Hz以上;而且齿轮啮合过程中还经常存在一定程度的冲击现象,其响应频率更高。普通电涡流传感器的频响达不到这一要求。因此齿轮振动测试必须采用加速度传感器在轴承或齿轮箱体上测取其振动信号,且整个测试系统的频响范围必须足够高。
2)较强的非线性。齿轮回转过程中,其刚度不断变化,呈现出较强的非线性,因此齿轮振动经常呈现出某些非线性特征。同时由于存在调频调幅现象,在高频的啮合频率两旁,还经常分布着一系列的以主轴回转频率为间隔的边频带,所以对高频下频率分辨率的要求也很高。
3)较大的噪声干扰。齿轮振动信号的传递路径较复杂,经过了轮齿一轮毅一轴一轴承一轴承座一传感器,最后传入故障诊断系统中。一方面引入了大量的噪声干扰成分,另一方面一部分高频信号迅速衰减,降低了信噪比。因此要提高齿轮诊断的准确率,必须首先对测得的信号进行降噪处理。
c5)故障源分析:制造与安装误差、剥落和裂纹等故障会直接成为振动的激励源,这些激励源都以齿轮轴的回转为周期,齿轮振动信号中含有轴的回转频率及其倍频。故障齿轮的振动信号往往表现为回转频率对啮合频率及其倍频的调制,在谱图上形成以啮合频率为中心,两个等间隔分布的边频带。由于调频和调幅的共同作用,最后形成的频谱表现为以啮合频率及其各次谐波为中心的一系列边频带群,边频带反映了故障源信息,边频带的间隔反映了故障源的频率,幅值的变化反映了故障的程度。齿轮箱在双馈式风力发电机组的作用是举足轻重的,而其故障率相对又偏高。所以风力发电机组中传动链的监测和故障诊断是以齿轮箱为重点展开的。
(d)主轴
在风力发电机的运行过程中,主轴起到连接风轮和增速箱的作用。由于风轮的低速旋转,并且直径大,受力面积大,在旋转的过程中主轴承受很大的扭矩作用。由于齿轮箱的制造和安装误差,齿轮箱在工作的过程中有较大径向和轴向振动,同时主轴为锻造件,在加工的过程中,有可能出现细小的锻造裂纹。在长期的振动过程中会对主轴产生疲劳损伤,使裂纹扩展,最终将导致断裂事故发生。
(e)主轴轴承
同大多数旋转机械相似,主轴轴承是受振动影响比较大的组件之一。在旋转过程中,主轴轴承的制造和安装误差均能使机组在运行的过程中产生振动。同时在工作过程中,轴承也将产生磨损,这也加剧振动。由于振动的产生,将在部件表面和内部产生裂纹,在轴承滚子及内外圈上产生剥离和点蚀等损伤,这又影响振动进一步加强,振动和机械损伤不断加强,最终使主轴轴承失效。
2、发电机失效
大型发电机在运行中可能发生各种内部故障和不正常运行状态,传统和比的应对措施是装设对应的继电保护装置进行反应并阻止事故的发生。由于结构上因,发电机保护远比传输线保护复杂,并且其部分故障是保护无能为力的“盲区”。已有的针对性保护装置与原理有待完善和进一步发掘之处也还很多。
3、故障诊断的基本方法
故障诊断技术经过十几年的迅速发展,到目前为止已经出现了基于各种不同原理的众多的方法。同以前相比,这些方法不论是检测性能、诊断性能,还是鲁棒性都有很大提高,而且对于线性时不变系统己经形成了相对较为完整的体系结构。所有的故障诊断方法可以划分为基于知识的方法、基于解析模型的方法和基于信号处理的方法三类,近年来又出现了一些新的方法,如基于离散事件的诊断方法和在线学习诊断方法。
所谓基于解析模型的故障诊断,就是通过将被诊断对象的可测信息和由模型表达的系统先验信息进行比较,从而产生残差,并对残差进行分析和处理而实现故障诊断的技术。所谓残差,就是与被诊断系统的正常运行状态无关的、由其输入输出信息构成的线性或非线性函数。在没有故障时,残差等于零或近似为零(在某种意义下)而当系统中出现故障时,残差应显著偏离零点。为便于实现故障的分离,残差应当属于下面二者之一。
1)结构化残差:指对应于每个故障,残差都有不同的部分与之对应,当诊断对象发生故障时,这些特定部分就由零变为非零。
2)固定方向性残差:指对应于每个故障,残差向量都具有不同的方向与之对应。一般而言,基于解析模型的故障检测与分离技术包括两个阶段:
(l)残差产生:就是利用一个适当的算法对系统的输入输出进行处理获取残差信号的过程;
(2)残差评价:就是利用适当决策函数和决策规则来确定故障发生的可能性的过程。
根据残差产生形式的不同,基于模型的FDI方法又可以分为状态估计方法、等价空间方法和参数估计方法。尽管这三种方法是各自独立发展起来的,但它们彼此之间却不是相互孤立的,而是存在一定的相互关系。等价空间方法与观测器方法在结构上具有等价性;而参数估计方法和观测器方法之间的关系,是指由观测器方法得到的残差包含了由参数估计方法得到的残差,因而两种方法在本质上是互补的。
根据等价空间方法、观测器方法和因式分解方法的设计参数之间的新型关系,并以此为基础提出了一种用于解决在基于等价关系和基于观测器的残差发生器的参数设计中遇到的典型问题的统一方法。基于状态的故障诊断方法主要包括两类:观测器方法和滤波器方法。而观测器方法又包括Leunberger方法、未知输入观测器方法、滑模观测器方法、模糊观测器方法、反推观测器法。
点击排行
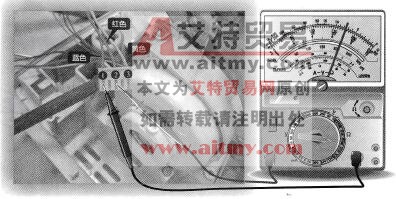