您现在的位置是:首页 > PLC技术 > PLC技术
采用PLC实现凸轮控制器控制逻辑的桥式起重机控
来源:艾特贸易2017-06-04
简介以继电接触器为基础的桥式起重机电路是个十分成熟的电路,在计算机没有应用到工业设备之前,以凸轮控制器实现大车、小车及副钩的操作,以主令控制器加继电器屏实现主钩的操作
以继电接触器为基础的桥式起重机电路是个十分成熟的电路,在计算机没有应用到工业设备之前,以凸轮控制器实现大车、小车及副钩的操作,以主令控制器加继电器屏实现主钩的操作控制,的确是科学的,并体现了工程的经济性。几十年来,凸轮控制器及主令控制器双方向多挡位的操作方式在起重设备中几乎形成了固定的模式。 但凸轮控制器操作中同时切换的触点毕竟太多,且切换的又多是电动机主电路的触点,为了切换大容量电流,触点都制造得厚重,这就为操作带来了阻力,增大了劳动强度。另一方面,凸轮控制器中有形的触点在频繁的切换中很容易出故障,给维修带来不便。那么能不能不用凸轮控制器但设法实现凸轮控制器在起重机各电动机主辅电路的逻辑连接关系呢?回答是肯定的,PLC能轻松地模拟各类电器的逻辑功能。现以大车的控制说明这个问题。 为了用PLC模拟凸轮控制器QM1,首先重读一下第一节中的表9-1,11个输入工作位置决定11组多触点输出组合关系的表。对于PLC来说,实现这样一张表时输入设备还是必要的,这可以是一个具有11个挡位,每l挡只有一个触点的主令控制器,表9-6给出了这样一个主令控制器的开合表,并为各挡位接通的触点安排了PLC的输人口。为了解决大电流切换的需要,PLC的输出必须连接接触器及继电器。它们是代替表9 1中凸轮控制器的各组触点的 只是这些触点在换用接触器后可以做的精简些,其中,向前、向后的四组触点可以用正转与反转两只接触器代替,切除两台电动机转子电阻的10个触点可以用5只接触器代替。这样就得到了用PLC实现模拟凸轮控制器的最终开合表9-7。在该表中PLC的输出口及输出口上连接的接触器编号已做了安排。 表9-6 具有11挡位,每挡只一个触点的主令控制器开合表 注:×-触头闭合。 表9-7 经精简后的模拟凸轮控制器开合表
注:×-触头闭合。 下面就是编一段程序实现输入口I0.0~I0.5及I1. 1~I1.5对输出口Q0.0~Q0.7及Q1.0~Q1.1的控制。程序的指令表如表9-8所示。编程的基本思想是用送数的方式,将输出口的控制状态要求送到一个数据存储器再转而由数据存储器控制输出口。例如,根据表9-7所示的向前第4挡(由表9-6知接通I0.4)的输出要求如图9-5所示,这时需传送到MW10中的数字正好为十进制数738。
图9-5 向前第4挡时输出控制字 表9-8 模拟凸轮控制器程序指令表
图9-6 3挡主令开关及增减电阻按钮示意图 以上方案的缺点是占用输入口太多,下面的方案使用图9-6所示的一个三挡位的主令开关及两只升降速按钮作为操作器件,使用PLC及接触器模拟凸轮控制器工作。三挡位的主令控制器的开合表如表9-9所示。主令控制器保留了凸轮控制器向前、向后操作时的机械互锁,且符合起重机操作工人的传统操作习惯,使用两只按钮进行升降速工作也很方便,使用这些操作器件时的梯形图如图9-7所示。其实现的控制要求主要有: (1)在按动接于I0.1或I0.2的按钮时,使切除电阻挡位存储器VB100中存储的数字在1~5间依顺序变化,以控制串入电动机转子中的电阻数量。这是使用加1及减1指令实现的,在VB100中的数值不小于5时可加操作,大于零时可减操作。 (2)电动机的方向控制由主令控制器实现,手柄置向前位时,I0.4接通,正转接触器工作,手柄置向后位时,I0.5工作,反转接触器工作。由正转到反转,或由反转到正转都必须经过零位,手柄在零位表示已关断正在运行的接触器,准备接通下一个接触器,同时手柄在零位时将切除电阻挡位存储器清零。 表9-9 3挡主令开关开合
注:×-触头闭合。
图9-7 模拟凸轮控制器梯形图 以上两点功能与原来使用凸轮控制器操作时各物理量变化的情况非常相似。
点击排行
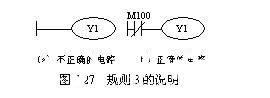