您现在的位置是:首页 > PLC技术 > PLC技术
使用S7-200 PLC控制水电站油压装置的初步设计
来源:艾特贸易2017-06-04
简介一、油压装置自动化的必要性与控制要求 油压装置是水电站的重要水力机械辅助设备,它产生并贮存高压油,是机组启动、停止、调节出力的能源;若水轮机蜗壳进口前设有蝴蝶阀,油
一、油压装置自动化的必要性与控制要求 油压装置是水电站的重要水力机械辅助设备,它产生并贮存高压油,是机组启动、停止、调节出力的能源;若水轮机蜗壳进口前设有蝴蝶阀,油压装置也是该阀的操作能源;当压力油槽油压事故性降低时,水轮发电机组将危险的失去操作能源,应有防护措施。油压装置的重要性与现代化潮流决定了用高新技术实现油压装置自动化的必要性。 油压装置自动化,应满足下列要求。 (1)水轮机组在正常运行或在事故情况下,均应保证有足够的压力油供机组及蝴蝶阀操作使用,应考虑在厂用电消失时有一定能源储备。此要求可通过选择足够的压油槽容积与适当的控制程序来解决。 (2)不论水轮机组处于运行状态还是停机状态,油压装置均应处于准备工作状态,亦即油压装置的自动控制是独立进行的,是由本身条件——压油槽中油压信号来实现自动化的。 (3)在水轮机组操作过程中,油压装置的投入运行是自动的,不需值班人员的参与。具体地说,当压油槽的油压降至油压下限(例如3.75MPa)时,启动工作螺杆油泵补油,压力提升至油压额定值(例如4.00MPa)时停止油泵工作。 (4)油压装置应设置供油的油泵电动机组,当工作螺杆油泵发生故障或者操作用油量急剧增长而造成压油槽油压过低(例如3.60MPa)时,启动备用螺杆油泵补油,压力提升至油压额定值(例如4.00MPa)时停止备用油泵,压油槽油压过低要求备用油泵投入时应发出报警信号。 (5)当油压装置发生各种罕见故障而造成压油槽油压下降至事故低油压(例如2.70MPa)时,应迫使水轮发电机组事故停机,事故停机时应发出报警信号(在主机控制程序中也应考虑)。注意,这里的起动主机事故停机之压油槽事故低油压值的整定应比可操作水轮机组的最小油压值大出一定量值,确保水轮机导叶在油压“崩溃”前能够全关,另外负曲率导叶的采用有利于这一问题的改善。 (6)油压装置的压油槽应选择合适的油气体积比K,经验证明一般取1:2,这是因为K值大时,由于操作放出等体积的油量后会造成压油槽油压更大的下降。今设压油槽容积为V,其中油占KV/(1+K),气体占V/(1+K),又设P、(P-△P)是放出△V体积油量前后的压油槽油压,代入玻意耳定律得:PV/(1+K)=(P-△P)[V/(1+K)+△V],从而△P=P△V/[V/(1+K)+△V],显然K越大,△P将越大。另一方面,K太小,将没有足够的压力油量,此处可结合第(1)点考虑。在油压装置运行中,由于微量气体不断地“溶”于油中,较长时间后会造成K值增大,为此应引用高压空气自动实行缺失补气(为相对“干燥”,故可考虑多级压力供气)。具体地说,当压力油槽油位上升至34%刻度并且油压下降至3.95 MPa时,打开可控气阀向压油槽补气;当油压上升至4.05 MPa或者压力油槽油位降至31%刻度时,关闭可控气阀停止补气。 (7)“补油”与“补气”两个进程互相闭锁,即“补油”时不“补气”、“补气”时不“补油”。 (8)为使“工作油泵”、“备用油泵”的总运行时间不致相差悬殊,引入“轮岗”思想,考虑工作油泵运行次数多于备用油泵运行次数达88次后轮换“工作油泵”与“备用油泵”的角色,此可巧妙利用S7-200的SWAP指令实现。 二、油压装置S7-200 PLC控制系统的硬件设计 经世界各国40多年的发展与完善,PLC已成为最重要、最可靠、应用场合最广泛的工业控制微型计算机,于是这里用PLC控制水电站(厂)油压装置。 系统控制两台补油螺杆油泵电动机组(一台工作、一台备用)、一只补气电磁阀(其ZT电磁铁有开启和关闭两个线圈,可不带电工作)、一只油压过低报警指示灯、一只油压事故低报警指示灯。系统有1个压油槽油压测量输入点(模拟量输入)、1个压油槽油位测量输入点(模拟量输入)、1个起动按钮SB1的输入(数字量)、1个停止按钮SB2的输入(数字量);2个补油油泵电动机组的输出(数字量)、1个补气电磁阀开起线圈的输出(数字量)、1个补气电磁阀关闭线圈的输出(数字量)、1个油压过低报警指示灯的输出(数字量)、1个油压事故低报警指示灯的输出(数字量)。合计:整个系统需要数字量输入2点、数字量输出6点、模拟量输入2点。选择CPU 222型的控制器,其DI/DO为8/6+78点、AI/AO为10点,可满足控制系统的点数要求;如果还有其他输出点,比如油压过高时报警,则应进行点数扩展。 在信号采集方面,选择国产AK-4型量程为5MPa、输出信号范围为4~20mA、输出接口为RS485的压力变送传感器2只(1只投入运行、1只作物理备用)及承压油位传感器1只(例如MSL-A隔离式液位变送器采用进口高品质的隔离膜片的敏感组件加放大电路,输出4~20mA二线制标准信号,封装于不锈钢外壳中),与S7-200 PLC共同组成硬件系统,传感器的电源应以不超载为原则作考虑。 S7-200 PLC输入/输出点地址分配见表4-1。 表4-1 S7-200 PLC输入/输出点地址分配 三、油压装置S7-200 PLC控制系统的程序设计 1.压力油罐压力折算 当测得压力油罐压力达到量程顶值5MPa时,LED-800变送器的电流为20mA,AIW(Y)的数值约为32767,每毫安对应的A/D值约为32767/20。测得压力为1MPa时,LED-800变送器的电流应为4mA,A/D值约为(32767/20)×4=6553.4。被测压力为1~5 MPa时,AIW (Y)的对应数值约为6553.4~32767,由此得出1kPa对应的A/D值大约为( 32767-6553.4)/(5000-1000)≈6.55,由此得出AIW (Y)的数值转换为实际压力值(单位为kPa)的计算公式为 IW2的值= [(AIW (Y)的值-6553)/655]×100 + 1000 (kPa) 2.压力油罐油位折算 设液位变送器的电流为20mA时,压力油罐油位顶高程( 40%)对应数值为32767,每毫安对应的A/D值约为32767/20 - 1638。测得油位为10%时,液位变送器的电流应为4mA,A/D值约为(32767/20)×4 = 6553.4。被测油位为10%~40%时,AIW (W)的对应数值约为6553.4~32767,由此得出1%油位对应的A/D值大约为(32767-6553.4)/(40- 10) =873.8,由此得出AIW (W)的数值转换为实际油位百分比的计算公式为 IW4的值=[AIW(W)的值-6553]/874+10(油位百分比) 3.控制程序流程 油压装置自动化控制程序流程如图4-1所示。
图4-1 油压装置自动化控制程序流程图 4.控制程序 编写如图4-2所示油压装置控制程序梯形图(供参考)。
图4-2 油压装置控制程序梯形图 油压装置控制程序语句表如下所示。
5.程序说明 启动油压装置后,初始化时把数1和0分别传送给VB2010和VB2011。读取压力油槽油压与油位,若油压低于“补油”油压下限值置位“工作油泵”投入标志,若油压低于“补油”油压过低值置位“备用油泵”投入标志。V2010.0=1、V2011.0=0时,1号油泵机组为“工作”、2号油泵机组为“备用”;V2010.0=0、V2011.0=1时,1号油泵机组为“备用”、2号油泵机组为“工作”。若1号“工作”次数比2号“备用”次数多88,交换VB2010与VB2011中的内容,V2010.0与V2011.0易位,实现“工作”、“备用”轮岗,即转为l号“备用”、2号“工作”;若2号“工作”次数比l号“备用”次数多88,再度交换VB2010与VB2011中的内容,V2010.0与V2011.0易位,再度实现“工作”、“备用”轮岗。当油压低于3.75MPa时,“工作油泵”投入运行,若某些情况下油压仍然降低,当低于3.60MPa,“备用油泵”投入运行,直至油压恢复到4.OOMPa时切除“工作”、“备用”油泵。油压过低由Q0.4报警,油压事故低由M50.0迫使水轮机组事故停机并由Q0.5报警。油位高于上限并且油压低于“补气”油压下限时由Q0.2开启电磁补气阀,油位低于下限或者油压高于“补气”油压上限时由Q0.3关闭电磁补气阀。停止信号用来关断1号和2号油泵电动机组的电源并关闭补气电磁阀。 油压装置自动化是十分必要的,分析油压装置得出控制要求后,可确定S7-200 PLC控制系统的I/O点数与硬件,绘出控制过程流程图(系统简单也可不示出)并编制程序。
点击排行
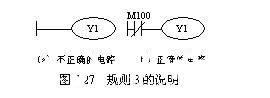