您现在的位置是:首页 > PLC技术 > PLC技术
东芝EX40H型PLC在储丝生产线系统控制中的应用
来源:艾特贸易2017-06-04
简介一、应用背景与需求 储丝生产线的功能是将上道工序已加工成的烟丝,按照不同的规格型号及不同等级分别送往指定的储丝柜储存并加以均匀混合。然后,根据需要将不同类型的烟丝送
一、应用背景与需求 储丝生产线的功能是将上道工序已加工成的烟丝,按照不同的规格型号及不同等级分别送往指定的储丝柜储存并加以均匀混合。然后,根据需要将不同类型的烟丝送往指定的卷烟生产线。 储丝生产线现场布置如图7.21所示,整个生产线由多个储丝柜、进料输送带、分配行车及分配带、铺料行车及辅料带、出料带及出料振槽等组成,其中每个储丝柜可以储存不同品种的烟丝,图中1~6序号分别表示一个储丝柜。 图7.21 储丝生产线现场布置图 本例针对卷烟生产中储丝生产线的控制问题,讨论PLC在其中的应用,包括控制系统的构成及控制程序设计等。 二、储丝生产线PLC控制系统的设计 1.工作过程分析 储丝生产线的工作过程如下。 ·烟丝通过进料输送带进入横跨于储丝柜之上的分配行车,分配行车是按X方向做往返运动的,并可根据指令自动定位于指定储丝柜的上方。烟丝由分配行车上的分配带传入储丝柜中铺料行车的铺料带上。铺料行车是按Y方向做往返运动,伴随着铺料行车在储丝柜中往复运动,铺料带正反转,将带上烟丝落入柜中并在柜中铺成一条线。 ·一条线铺完后,铺料行车停止。分配行车启动并步进一段距离停止。铺料行车又开始铺第二条线。如此往复,直至在柜中铺一层烟丝。第一层铺完后,分配行车反向步进,铺料行车开始铺第二层。直到储丝柜满,进料系统停止。接到另一条指令后,分配行车会重新寻找指定储丝柜进行进料。 ·生产线出料时,被指定的储丝柜的底带启动。底带可根据指令调整出料速度。烟丝通过底带进入出料振槽,分别送往下道工序。 整个生产线可以通过几个出料口同时出料,甚至可以在同一柜中进出料同时进行。生产线工艺流程如图7.22所示。 2.PLC功能及系统构成 根据设计任务书要求,PLC应满足以下功能。 ·进料时,根据与传感检测信号的应答,可以准确定位分配行车。 ·铺料时,完成分配行车、铺料行车、铺料带的时序动作及循环联锁控制。 ·出料时,完成系统各电机的顺序控制并随时记录出料完成情况。 ·随时对整个系统的动作进行监测,出现故障后可自动对相关部分进行保护。 ·可在工艺流程显示屏上随时显示生产流程及故障发生点,并有故障的声光报警。 根据上述功能,构成PLC控制系统总框图,如图7.23所示。
图7.22 生产线工艺流程
图7.23 控制系统总框图 根据控制系统的要求,选用两台东芝EX40H型PLC作为控制主机,并配两台扩展单元。I/O总点数可达140个。 为了满足分配行车、铺料行车的往复运动及分配行车的进料定位,系统选用了20只无接触式感应接近开关。进料满和出料完的信号是通过装在储丝柜内上、下部2对光电开关来完成的。整条生产线装有12对光电开关。 工艺流程显示屏上各动作点的显示选用发光二极管。该显示屏不仅可以显示生产线工作状态,而且可以通过发光二极管的闪烁及声讯系统随时显示故障发生点。 表7.5给出了PLC的I/O点分配表。 表7.5 I/O点分配表
该系统除设计了PLC自控系统外,还设计有手控系统。手控系统便于调试和维修。同时,由于它脱离了PLC控制,在生产线自动系统出现故障时,可以作为系统的降级使用。 三、储丝生产线PLC控制梯形图设计 生产线有手控和自动控制之分。在手控状态下,整个系统完全脱离PLC控制,PLC所有输出点皆不工作。操作者可根据主控柜面板上各操作开关分别控制24台电机运行。当控制开关选择自动运行后,PLC接通电源,并通知各行车运行至初始位置待命。图7.24为系统的控制流程图,说明如下。
图7.24 软件系统总框图 ·当PLC接到某号柜进料的命令后,首先指挥分配行车向该柜前进,并根据该柜位置接近开关的信号定位于该柜上方。然后,分别延时3s启动进料输送带、铺料行车、铺料带、分配行车和分配带各电机。延时的目的是为了避免系统的局部堆料。 ·当PLC接到铺料行车到达极限位置传感信号后,通知铺料行车反向运行。同时命令分配行车再启动并步进2So分配行车按设计任务书要求如此步进6次。 ·PLC收到分配行车极限位置的限位信号后,指令其反向步进。至此,进料程序开始循环。在循环过程中,料满传感器不断将信号送往PLC。PLC接到料满信号后,指示报警系统工作。1分钟后,通知进料系统将各电机间隔10s分别关机。软件中还应设置各储丝柜进料的互锁指令,即当PLC在给某号柜进料过程中,不再接受其他柜进料的指令。 ·当PLC接到某号柜出料命令后,每间隔3s启动出料口外各电机。如1号储丝柜外有两级出料振槽和一个风力送丝出料电机,应间隔分别启动。然后启动出料拔辊。电机运行3s后,再启动出料底带运行。 · 出料过程中,PLC始终与出料传感器应答信号,监视出料情况。当PLC收到由光电开关送来的出料完信号后,继续运行1分钟后自动间隔停各电机。软件中将6个储丝柜的出料程序处理为“与”的关系,即各储丝柜可以同时分别出料,互不影响。由于该系统庞大,所以程序也较为繁琐。软件设计中多次采用了时间控制、时序控制、各部分互锁和控制循环。 图7.25所示为1号柜进料程序梯形图。图7.25中,符号L均为内部锁存器,其功能为对特殊信号的记忆。符号R均为内部继电器,其功能为程序内部的转换与连接。
图7.25 1号柜进料程序梯形图 四、总结与评价 储丝生产线在启动后连续工作时间长,环境温度温差大,对控制系统的可靠性要求高。选用PLC作为控制器,可以适应系统的工作特点和运行环境,并具有控制灵活的特点。此外,系统设计中选用的所有传感器均选用无接触式器件,避免了开关次数过多对系统可靠性的影响;系统除设计了PLC自动控制系统外,还设计有手控系统,手控系统可便于调试和维修,同时由于它脱离了PLC控制,在生产线自动系统出现故障时,可以作为自动控制系统的备份使用。 应用表明,储丝生产线的PLC控制系统可以达到长时间连续、可靠工作的要求,PLC在类似生产线的自动控制中有广泛的应用前景。
点击排行
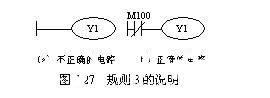